Mastering Six Sigma at Inno-Xellence Academy: Your Path to Excellence
Are you ready to take your skills to the next level and drive significant improvements in your organization? At Inno-Xellence Academy, we offer a comprehensive Six Sigma training program designed to equip you with the tools and knowledge needed to excel in today’s competitive environment. Here’s a detailed step-by-step guideline for implementing Six Sigma methodology, structured around its DMAIC framework (Define, Measure, Analyze, Improve, Control)
1. Define Phase
Goal: Define the problem and the project scope.
Steps:
- Identify the Problem: Clearly define the problem your team is trying to solve. Use a Problem Statement to capture what the problem is, why it’s important, and its impact on business.
- Set Objectives: Define clear and measurable goals that align with customer needs and business strategy.
- Form the Team: Assemble a cross-functional team with roles like Green Belts, Black Belts, process owners, and key stakeholders.
- Voice of the Customer (VOC): Gather customer feedback to understand expectations and identify Critical to Quality (CTQ) attributes.
- Develop Project Charter: Create a charter detailing the problem statement, project scope, team members, resources, and high-level timelines.
- Create Process Maps: Create SIPOC (Supplier, Input, Process, Output, Customer) diagrams to visualize the process from a high level.
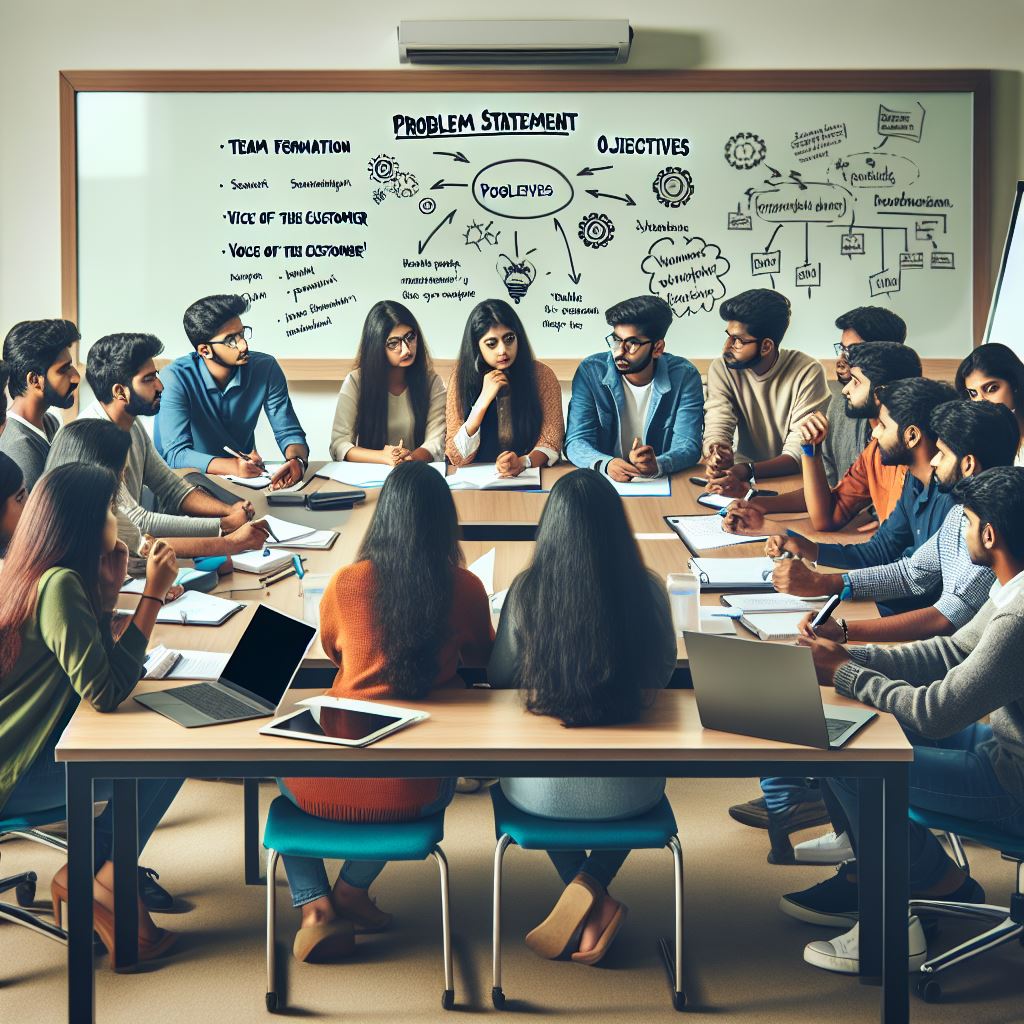
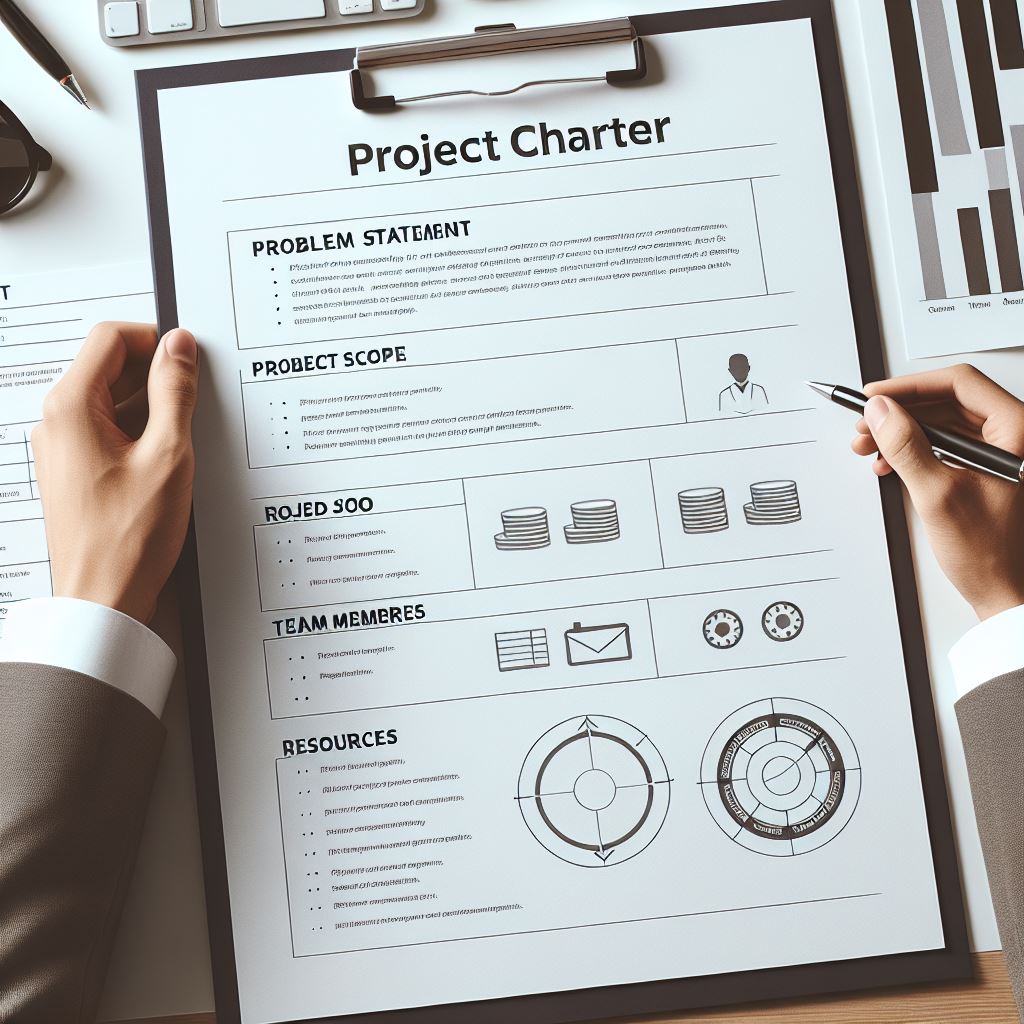
2. Measure Phase
2. Measure Phase
Goal: Measure the current process and establish baseline performance.
Steps:
- Define Metrics: Select relevant metrics (KPIs) that will be used to measure process performance and success criteria.
- Data Collection Plan: Develop a detailed plan for gathering data from the process, identifying sources, methods, and required data types.
- Validate Measurement System: Ensure that the tools used for measuring are accurate and reliable. This can be done through Measurement System Analysis (MSA).
- Establish Baseline Performance: Collect data from the current process and determine baseline performance. Use statistical tools like histograms and run charts to visualize this data.
- Calculate Process Capability: Determine how well the process meets specifications using process capability analysis (Cp, Cpk).
3. Analyze Phase
3. Analyze Phase
Goal: Analyze data to find root causes of defects or variations in the process.
Steps:
- Identify Potential Root Causes: Use tools like Fishbone Diagrams (Ishikawa), Pareto Analysis, and Brainstorming sessions to list potential causes.
- Data Analysis: Use statistical techniques such as hypothesis testing, ANOVA, or Regression Analysis to investigate relationships and test potential causes.
- Process Mapping and Analysis: Use tools like Value Stream Mapping to identify non-value-added steps (waste) and understand bottlenecks.
- Root Cause Verification: Validate suspected root causes with further testing, such as conducting experiments or using 5 Whys and FMEA (Failure Modes and Effects Analysis).
4. Improve Phase
4. Improve Phase
Goal: Implement and verify solutions to address root causes and improve the process.
Steps:
- Generate Improvement Ideas: Brainstorm solutions to eliminate the root causes. Use Lean principles like reducing waste and improving flow where applicable.
- Develop Solution Strategies: Evaluate alternative solutions using criteria such as cost, ease of implementation, and potential impact.
- Pilot Test Solutions: Before full-scale implementation, test your solutions in a controlled environment to evaluate their effectiveness. Perform a Design of Experiments (DOE) if applicable.
- Implement Improvements: Roll out successful pilot solutions across the process. Use project management tools to ensure smooth implementation.
- Process Optimization: Optimize the process further by standardizing the new procedures and integrating changes into the workflow.
5. Control Phase
5. Control Phase
Goal: Sustain the improvements and ensure that gains are maintained over time.
Steps:
- Develop a Control Plan: Create a detailed plan that includes procedures, metrics, and tools for monitoring the improved process.
- Implement Statistical Process Control (SPC): Use control charts to continuously monitor process performance and quickly detect any deviations.
- Standardize Procedures: Document new processes in standard operating procedures (SOPs) to ensure consistency in execution.
- Train Employees: Provide training to employees and stakeholders on the new processes, ensuring that everyone follows standardized procedures.
- Monitor and Audit: Schedule periodic audits to check the process’s adherence to the new standards, and measure the success of improvements against the original objectives.
- Continuous Improvement: Foster a culture of continuous improvement by encouraging ongoing analysis and small, incremental improvements even after project completion.
Key Six Sigma Tools:
- DMAIC: Framework used for process improvement.
- SIPOC Diagram: Provides a high-level view of the process.
- Pareto Chart: Identifies the most significant factors.
- Fishbone Diagram: Helps identify root causes.
- Process Capability Analysis: Evaluates how well a process meets specification limits.
- Control Charts: Monitors process stability over time.
- Hypothesis Testing: Used for decision-making based on data analysis.
A Step-by-Step Guide to Driving Excellence at Inno-Xellence Academy
This step-by-step approach ensures that Six Sigma projects are handled systematically to achieve process improvements and reduce defects, enhancing overall quality and performance.
Join us at Inno-Xellence Academy to master these techniques and drive excellence in your organization!